Pitch variation in heliciel
Design: propeller, turbine, screw, aerial, marine, turbine, tidal, wind, kaplan, foil, wings, 3D. Discover heliciel software:
The variable pitch propeller pitch variation
Understand and master the variable propeller pitch:
- The common expression propeller "variable pitch" means a propeller whose pitch varies along the length of the span of the blade, and which can vary the collective pitch of all sections through the blade assembly on an axis .
- A fixed pitch propeller, corresponds to a single operating point defined by the speed of rotation and the velocity of the fluid. It is therefore understandable that a generation of technicians is committed to achieve the variable pitch propeller..
The impeller is similar to a screw which converts the rotational motion of the motor in motion propulsion, translation of the aircraft or boat ; it transforms circular motion into linear motion,as the group consisting of wheels and transmission components for land vehicles. But the latter are supported on a solid surface(road, rail) While the propeller is based on a fluid medium, so deformable. The propeller is similar to a screw, but the parallel-propeller is only valid to some extent. If the propeller could be considered as the bolt is screwed into a nut, it would have only one travel speed for a given speed of rotation. In fact fluency allows the propeller to rotate while the translational speed of the aircraft is not one that matches the pitch. In short, from the standpoint of the propeller, the "elasticity" of the fluid has the advantage: range, operational flexibility propeller, and disadvantage: loss of efficiency (slip).
- We can say that the problem of variable pitch propeller is an aspect of the general problem of the gear change. Indeed, whatever the vehicles in question, and the environments in which they move, technicians have always tried to approach this result: constant value and as high as possible of the product energy received at the output of the engine and performance of propellant system. So two types of approaches: working on the motion transmission system which connects the engine to the propeller, or working on the propeller.
The transmission system is theoretically a gearbox which is not to be considered in aviation -too heavy and must remove the engine torque to move from one gear to another. It remains to consider the propeller to get the constancy of the product mentioned above, we have several elements: the blade surface, the general shape of their profiles the curvature of the profile, the pitch of the blade. We can act on the blade area either by varying the diameter (for example, the blade foot which is screwed or unscrewed), or by varying the depth of the blade (propeller with slot, for example) and it was the case of the propeller Clarence Holman, conducted in the United States, and included a leading edge flap, as it was for the wing of the Potez 36.Or else as follows: on the same motor, two propellers rotating in opposite directions for the takeoff phase, ascent, slow flight; for rapid flight, Only one propeller operation, the other turning freewheel. And we find here the case of French propeller Salaun ; it consisted of two identical propellers, mounted on the drive shaft, one behind the other; both propellers executed the rotational movement of all propellers but,front propeller had the ability to slide on the shaft, whereby the slot between the two propellers varied automatically. We can act on the profile, with a system that changes the flow around the profile. Breguet around 1930, realized a propeller with hollow blades: drilled holes along the intrados,caused the effects of nozzle on the distribution of flow. Difficult to achieve, as the previous solution.
- The ideal solution: the propeller with diameter, profile, area and pitch variables simultaneously in flight. Only one of these four conditions is satisfied by the variation of pitch . This explains why the performance of the propeller at take off, is less than what it is while cruising.
hydraulic diagram of a variable pitch system:
sectional view of a variable pitch propeller
The evolution of the variable pitch propeller: Considering the range of pitch::
- Propeller with two pitch (start and cruise)
- Multiple pitch propeller.
- Multiple pitch propeller,including setting flag.
- Multiple pitch propeller, including setting flag , and reversibility.
- Manually controlled propeller.
- Propeller with automatic operation.
- Energy taken from motor (mechanically driven propellers and hydraulic control)
- Electrical energy. a) rotating engines b) stationary engines.
- Aerodynamic Energy (wind turbine, torsion bars).
- compressed air
- rods.
- endless screw.
- gear rack.
- bevel gears.
With this type of control, the energy required to change the pitch is taken from the engine ; For this a clutch is mounted between the motor housing and the control system of the blades (integral with the driving shaft) ; when the clutch is operated, it ensures the variation of pitch of the propeller via one of the control systems which it just mentioned and reductor. The clutch can be operated either by hand or by using couplers, these being electromagnetic or pneumatic.The electrical control:
Two types of achievement : mobile motor fixed at the shaft end driven by the propeller ; moteur fixe. stationary engine. In both cases, the rotary motion of the electric motor is converted, by a reductor, in a rotational movement of the propeller blade. With electric power, is used a source independent of the engine, which is an advantage and a disadvantage. The control is easy to achieve with these propellers, but this system has a certain fragility, especially in the case of the rotary electric motor, and a large amount of power is required to achieve a fast pitch variation.The hydraulic control :
As in the case of the mechanical control, this type of propeller does not use any energy easement :it uses the oil in the circuit which supplies the motor.. three variants : with fixed piston and moving cylinder (Rotor),Fixed cylinder and piston - single acting - Mobile (Hamilton) fixed piston and cylinder - double acting - Mobile. In the realizations having a piston which works only on one side, the propeller pitch are two in general, one of the pitch being obtained by the pressure of the oil on the piston, so that it is the centrifugal force which brings the propeller to another pitch. The "flag" position can be easily obtained with the double-acting pistons.the control
Since the beginning, the manual control of the pitch appeared to be temporary. The pitch should vary automatically, either to continuous manner, or almost instantly. Since the beginning so it was implicitly assumed that the variation of pitch required an automatic regulator.
- We have seen that to each operating point matches an optimal blade angle of attack,It is therefore necessary that the whole: Propeller engine, includes an automatic regulator,system whose role is precisely to link every moment - and automatically - blade pitch, to engine rpm.Conventionally, the controller has a centrifugal device acting, by a relay, on the control for varying the pitch : when the speed of the aircraft or boat tends to increase, the controller increases the pitch...
Despite their additional complexity, variable pitch propellers offer certain advantages for boats: systems of pitch variation are many, observe two types pitch variation:
- self pitching propeller: used on small boats and sailboats.
the "self pitching propellers" current are derived from the work of Griffith (1849). Forward, the propeller blades, whose axis allows rotation, come under the influence of a lift and axial misalignment, to put into abutment with their operating pitch. If the propeller shaft stops rotating the blades set in flags position and reduce drag when the boat is under sail. When in reverse the blades come to into abutment pitch. It should be noted that the positions of angles backward and forward are preset. It can not be adjusted during operation .the angle of incidence is optimum only if the preset angle into abutment matches to the operating point of the propeller at this angle
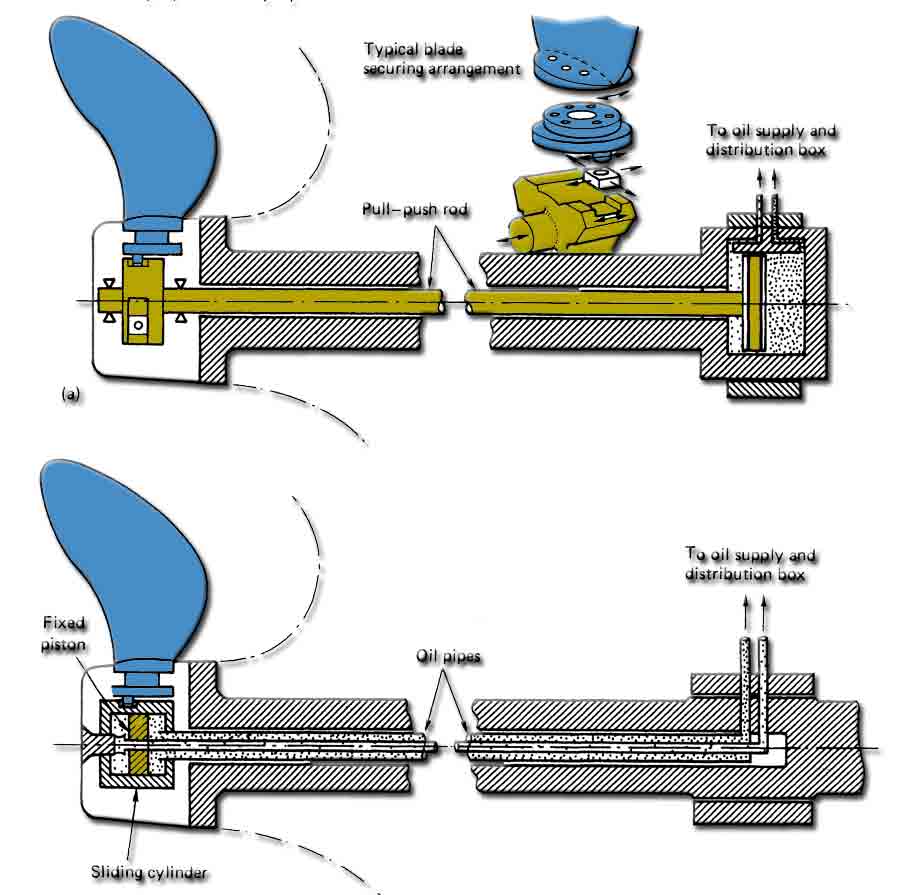
A simple glance at the evolution of sales of variable pitch propellers gives us an idea of the place that took the system in shipbuilding:
Pitch variation of wind turbine tidal turbine
Wind turbines use the pitch variation mainly as a means of regulating their power:The high wind speeds are certainly very interesting from an energy point of view but they are infrequent. So needless to oversize wind for these high speeds. Because the price of some components increases rapidly with the power they have to transmit. That is why modern wind turbines are designed to achieve their rated power at about 15 m / s and are stopped automatically to 25 m / s. To limit the power increases with the cube of the wind speed, it is necessary to establish a system of regulation.Briefly, we distinguish two kinds:
- Fixed pitch : the blades are rigidly mounted and it is the geometry of the blade that is designed to take advantage of the aerodynamic stall in order to bring down the aerodynamic efficiency and maintaining power, almost constant Over the wind speed control (stali control). This system has the advantage of being simple, so reliable and less expensive. This compensates for its slightly worse performance than the variable pitch
- Variable pitch :The blades can be moved about their longitudinal axis. We then say that the propeller is variable pitch and a mechanism increases pitch when the wind speed becomes too high, so as to reduce the lift and therefore the driving torque (pitch control). It is more complex, but it allows finer control and has a better performance. An advanced control system determines the best position of the blades to the wind and directs the system to run the hydraulic positioning.
- It reduces the load on the structures in high wind conditions
- The startup speed is reduced. The rated power is never exceeded. This ensures "clean" output power.
- Dust that settles on the blades is regularly removed, avoiding costly cleanups.
- Adjusting the angle of the blades according to the site is not necessary.
- This is a security system against over-speed of the turbine.
- The output of the machine adapts to the network load, avoiding expensive and fragile discharge systems.
- Changes in air density are compensated.
- It avoids the installation disk brake to slow the turbine in strong wind conditions, thereby reducing maintenance costs and avoids efforts on key components in the process of reducing speed.
Regulating the rotational speed is also achieved by means of electric motors, for the great powers. In this case, use is made either of individual motors for each blade, synchronized with each other,either a single electric motor for the whole of the blades. The stepper motors geared down, actuate gears which mesh with the gear wheels fixed to the root of each blade. The control is done through the primary shaft.Whatever the method used, The device control the pitch permanently. It facilitates starting giving. to the blades, a pitch angle sufficient. Between wind speed startup and rated wind speed , it makes the machine work at its maximum aerodynamic efficiency. Between the nominal wind speed, and maximum wind speed, it limits the power captured by increasing the pitch. When the wind speed reaches the maximum value, it stops the turbine blades by feathering